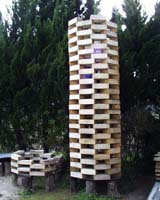 |
墨かけされた材を切り分けて1足分づつにします。角木どりされた材料は外に1つ1つ積み上げて下駄の塔を作ります。そして1年以上の時をかけて雨と太陽でゆっくりと乾燥させて行きます。
師走の頃にはアクが染み出して表面が真っ黒になります。そして桐独特の軽い木材へと変身しているのです。
この輪積みは雨がすべての材料にかかるように微妙なバランスで積まれていきます。綺麗に並んでいれば良いと言う訳ではないそうです。自然の力を最大限に利用できる形があみ出されていました。 |
|
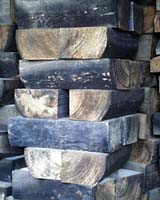 |
外で乾かされた材料は更に半年間以上を倉庫の中で乾燥します。
急激な乾燥をすると木の断面に割れが入ってしまいます。現代では、それを詰め物でごまかす事もされていますが、澤田氏は納得できない事はしません。
赤ちゃんより大切に扱って来たと奥様がおっしゃるほどに神経を使って、手をかけて乾燥させていきます。 |
|
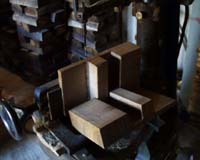 |
糸木挽き。
糸鋸を使い、角木を切り分けます。
2つになった瞬間にパラリと分かれるのは見物です。カーブを見事に回る鋸ですが、一朝一夕では出来る技ではなさそうです。「鋸に逆らわず回すだけですよ」とおっしゃっておられましたが・・・ |
|
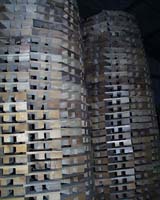 |
工場の一角には糸木挽きされた材料が 更に輪積みされていました。
本当に長い年月をかけて造られて行きます。 |
|
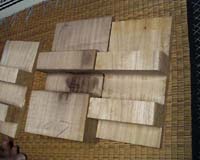 |
六枚鋸をかけると、いよいよ下駄らしい形になって来ます。
左がかける前、右がかけた後です。 |
|
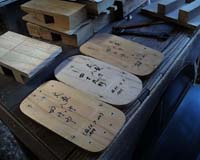 |
丸目の工程で使われる「型」です。
この形がそれぞれの下駄屋さんの特徴が出てくる部分です。勿論こちらの型は全て澤田氏の作られた物。
こうして揃った物が出来あがります。
「形」はデザインの柔らかさや力強さの度合いを決める物となります。 |
|
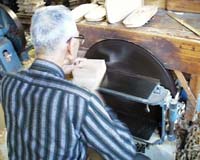 |
丸目の作業風景です。
簡単そうですが、「型」も桐材ですから少しでも削りすぎると「型」の形まで変わってしまいます。
|
|
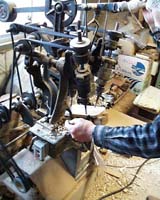 |
穴あけ。
鼻緒を通す穴を開けます。この穴を開ける角度が履いた時の歩き安さに関係しているようです。勿論、開ける場所が下駄のバランスを決める上でも重要な役割の1つですよね。 |
|
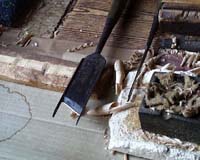 |
重納と言う道具です。
角のように出た部分を耳と呼び、真っ直ぐにそぐ為のガイドとなります。 |
|
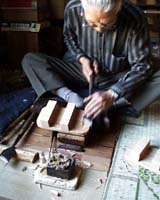 |
裏仕上げの8工程の内の1つ。
重納を使って裏仕上げを行っているところです。
腕もさる事ながら脚も職人技を会得していなければ上手く行きません。
右横から入る天然の太陽光線でなければ良い仕事が出来ないのだと語って下さいました。薄い削りくずは見事でかつおぶしのようです。
|
|
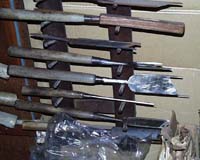 |
重納も1寸5分、1寸7分などサイズが色々ありました。
細いのは丸すきと呼ばれる道具です。 |
|
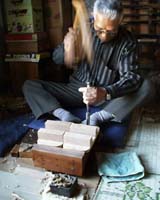 |
菊打ち。
鼻緒のつま先側の所に窪みをつける作業です。 |
|
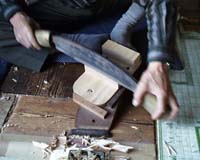 |
センと言う独特の道具を使って削っています。
力も必要なので75歳が限界だろうとおっしゃりながら見事な技を披露して下さいます。
既に歯の幅が決まっているので、確実に同じ厚みで削り出して行かなければ左右が違うサイズに仕上がってしまいます。 |
|
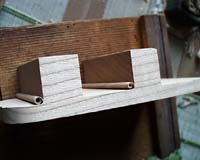 |
センを使った所で、一度撮影させて頂きました。
ロール状に成っている所が削られた物です。 |
|
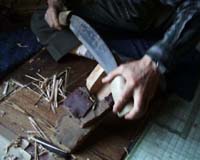 |
下駄の後ろの分部をセンで削っているところです。
この手仕上げが澤田氏の技の見せ所です。 |
|
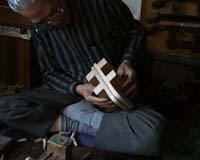 |
下駄の表に鉋をかけました。
今、表どうしを合わせて鉋のかかり具合を見ていらしゃいます。
フラットに成った2面は吸い付きます。ピッタリ合わせて片方を引き離すようにすると吸い付いてもう一方が付いて行きます。
滑らかな履き心地はこんな職人技に支えられていたのです。
この後、更にとの粉を付けて磨いたり、焼を加えたりして仕上げて行きます。
2年以上の時を経て、澤田氏に切り出された桐は 美しい下駄として命を貰うのです。 |
|